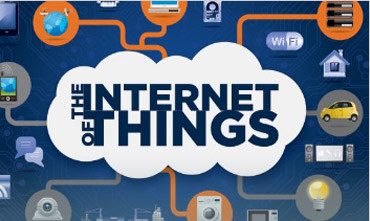
Manufacturing and The Internet of Things
The Internet of Things – IoT (Wikipedia) is the network of physical objects or “things” embedded with electronics, software, sensors, and network connectivity, which enables these objects to collect and exchange data.
The IoT has created a lot of conversations, some stating it’s all hype, some questioning it’s benefits more of something for the future and obviously the ones in support.
Now let’s not pretend here, the IoT is already here, we have smart houses, apps for lights, heating, music, etc. Recently, my neighbours installed a security system which allowed them to view, check, and switch their alarm on and off accessed from internet, this also alerted him to security issues around the property (the most important aspect). So we can’t say it’s not here already.
Now put this into the manufacturing environment.
Some renowned manufacturers have already started investing in hardware, software, and networking systems. Build the IoT infrastructure now to capitalise on its benefits.
I read in an article recently that GE anticipates $19 trillion in profits and cost savings projected over the next decade.
One major area I can see the benefit is Energy Efficiency. To be able to track all facilities, machines energy consumption on a granular level, this visibility will give feedback on a machines abnormal to normal status, something that we can action, countermeasure, control. It will highlight our waste, our areas for improvement, and better understanding of our costs and how to control them. And as stated this has to be a major benefit for manufacturing, something I certainly wanted as an Exec.
The ability to benchmark similar machines/resources, predict maintenance issues with surges in unusual energy consumption, highlighting the out of hours energy waste and being able to control and manage this. All of these will have a direct impact on the bottom line and this is just scratching the service.
The connectivity within production processes is another example, let’s say a machine is not running at optimal performance, this machine would send an alarm highlighting it’s situation to the production team, it could then slow itself down (as not to self-destruct) communicate with its upstream and downstream processes and slow them down limiting the amount of lost production and or downtime and controlling the standard in process stock.
Bosch’s Stefan Ferber stated “The Internet of Things allows for a new way of organising industry production: by connecting machines, warehousing systems and goods, we can create smart production systems that basically control each other without requiring any manual intervention.”
I will always remember the saying “ the Data will set you free” by allowing you to make “Informed Decisions”, can’t get much better than real time data, and that’s the possibility with IoT.
The Internet of Things global economic impact is massive. Approx. 25% of Global Manufacturers are already using IoT technology, this is expected to grow to 80% by 2025. In reading different articles/surveys most cannot put a definitive figure on the potential impact but the range is between $1.9 to $14.4 trillion dollars on the global economy.
Digital Manufacturing Stats from ASQ:
The American Society for Quality (ASQ) surveyed manufacturing companies that have digitised their processes and found astounding results:
- 82% increased efficiency
- 49% experienced fewer product defects
- 45% increased customer satisfaction
0330 311 2820
More Blog Posts
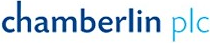
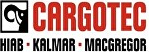
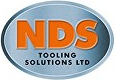

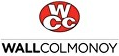
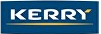
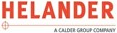
To leave me a message or book a return call at a time that suits you