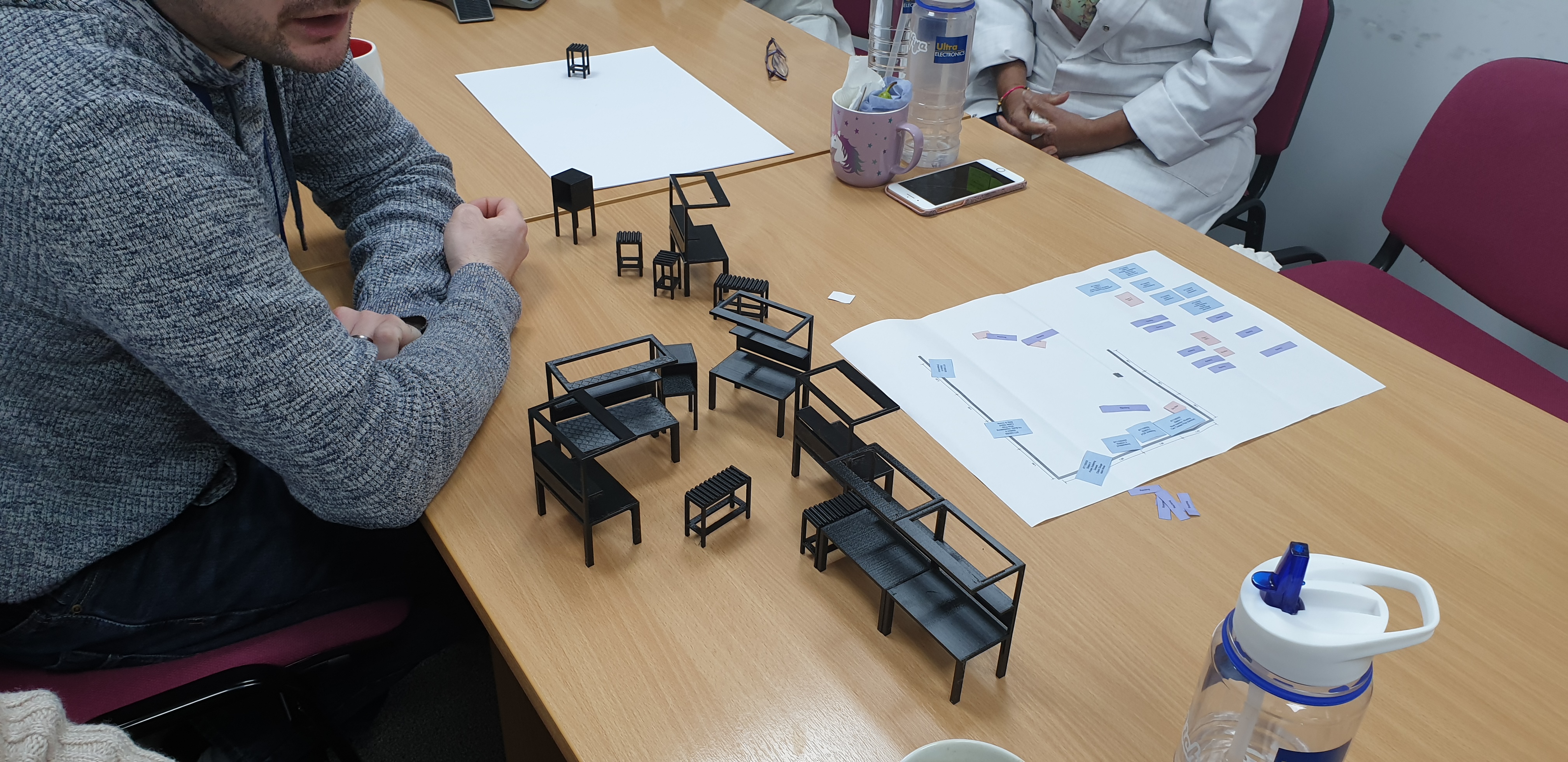
Beyond Machinery: Unlocking Human Potential in UK Manufacturing
In the bustling heart of the UK’s manufacturing sector, staying competitive isn’t just about modern machinery or cutting-edge technology. It’s about the people behind the processes, the efficiency of operations, and the culture that drives continuous improvement. If you’re a manufacturer looking to propel your business forward, embracing Lean Coaching and Mentoring could be the game-changer you’ve been searching for.
Imagine shaving weeks off your project timelines, cutting costs significantly, and fostering an environment where every team member is committed to excellence. This isn’t a distant dream—it’s the reality for many manufacturers who have harnessed the power of Lean Coaching and Mentoring. In a landscape where the slightest edge can set you apart from competitors, Lean methodologies offer a transformative approach to streamline operations, enhance quality, and boost employee satisfaction.
As someone who has walked the factory floors, engaged with teams at every level, and witnessed the profound impact of Lean Coaching, I can attest to its potential to revolutionise manufacturing processes and business culture. Let’s delve into how this personalised approach not only optimises efficiency but also cultivates a culture of continuous improvement, giving you a significant competitive advantage in the market.
Supercharge Project Performance and Efficiency
Time is money in manufacturing, and delays can cost more than just capital—they can erode customer trust and market position. Implementing Lean principles through 1-2-1 coaching can dramatically enhance project performance.
Projects Finish Over 20% Faster with Lean Coaching
When coaching is tailored to individual needs, it can identify bottlenecks that generic training often overlooks. For instance, during a recent engagement with a mid-sized manufacturer in Birmingham, we implemented Lean Coaching that reduced their average project completion time by 25%. By focusing on specific pain points, we eliminated unnecessary steps, allowing projects to move forward swiftly. This approach not only accelerates timelines but also instils a sense of ownership and accountability among team members, as they see the impact of their contributions.
Cost Savings Exceed 10% Compared to Conventional Management
Lean isn’t just about speed; it’s about doing more with less. By scrutinising every aspect of the production process, Lean Coaches help you identify and eliminate non-value-added activities. In my experience, manufacturers often discover surprising areas of waste—be it overproduction, excess inventory, or redundant processes. One client saved over 15% in operational costs within six months by streamlining their supply chain and reducing overstock. These savings can then be reinvested into other areas of the business, such as research and development or employee training, further enhancing the company’s competitive edge.
Identifying and Eliminating Non-Value-Added Activities
Non-value-added activities are like weeds in a garden—they choke the life out of productive processes. Through Lean Coaching, team members learn to spot these activities and address them proactively. For example, unnecessary movement of materials not only consumes time but also increases the risk of damage. By reorganising the factory layout for a client in Warwickshire, we reduced material handling time by 30%. This not only improved efficiency but also reduced the physical strain on workers, contributing to a safer and more ergonomic workplace.
Reduced Inventory Overhead, Overtime, and Lead Times
Lean coaching emphasises just-in-time production, which minimises inventory costs and ensures resources are utilised efficiently. A manufacturer we worked with was struggling with high inventory costs and frequent overtime. After implementing Lean practices, they saw a 40% reduction in inventory overheads and eliminated overtime in peak seasons, leading to happier employees and a healthier bottom line. This shift also allowed the company to be more responsive to market demands, as they could adjust production schedules without the burden of excess inventory.
Foster a Culture of Continuous Improvement
Implementing Lean isn’t a one-time fix—it’s about instilling a mindset of perpetual growth and enhancement throughout your organisation.
Building a Lean Culture Focused on Learning and Critical Thinking
A culture that values continuous improvement encourages employees to think critically about their work processes. By fostering an environment where questions are welcomed and experimentation is encouraged, you tap into a wellspring of innovation. In a recent project, we introduced daily stand-up meetings where team members shared insights on process improvements. This practice led to over 50 incremental enhancements within a year. These small, consistent changes accumulate over time, leading to significant improvements in efficiency and quality.
Developing Employee Skills and Boosting Satisfaction
Investing in your employees through coaching not only enhances their skills but also increases their engagement and satisfaction. Employees who feel valued and empowered are more productive and loyal. I recall a team leader who, through 1-2-1 lean mentoring, developed such confidence in problem-solving that they were promoted to operations manager within a year. This personal growth not only benefits the individual but also strengthens the organisation as a whole, as skilled leaders are better equipped to guide their teams through challenges and drive innovation.
Creating an Environment of Clear Expectations and Systematic Processes
Clarity is crucial in manufacturing. Lean coaching helps establish well-defined roles and expectations, reducing confusion and errors. By standardising processes, you ensure consistency and quality. At a facility in Ellesmere, the introduction of standardised work procedures decreased defects by 35%, directly impacting customer satisfaction. This consistency also builds trust with customers, as they can rely on the company to deliver high-quality products on time, every time.
Establishing Sustainable Improvements Through Embedded Learning
The goal of Lean Coaching and Mentoring is to make continuous improvement second nature. By embedding Lean principles into the fabric of your organisation, improvements become sustainable. One company I worked with integrated Lean training into their onboarding process, ensuring that every new employee contributes to the culture from day one. This approach not only accelerates the learning curve for new hires but also reinforces the company’s commitment to excellence and innovation.
Gain a Competitive Edge in the Market
Standing out requires more than just a quality product—it demands excellence at every operational level.
Producing Higher-Quality Products Faster
Lean methodologies focus on quality at the source, minimising defects and rework. By empowering employees to identify issues in real-time, you enhance product quality while reducing waste. A manufacturer in Coventry improved their first-pass yield by 20% after implementing Lean, leading to increased customer satisfaction and repeat business. This focus on quality not only strengthens customer relationships but also reduces costs associated with returns and rework.
Reducing Lead Times and Improving Customer Service
Customers value reliability and speed. By streamlining processes, you can reduce lead times significantly. One of our clients managed to cut their delivery times in half, which not only satisfied existing customers but also attracted new ones who required quick turnaround times. This agility in responding to customer needs can be a decisive factor in winning new business and retaining existing clients in a competitive market.
Driving Innovation Through Optimised Workflows
Lean isn’t just about cutting waste—it’s about creating space for innovation. By removing unnecessary tasks, employees have more time to focus on creative solutions and improvements. In one case, a team’s workflow optimisation led to the development of a new product line that opened up additional revenue streams. This ability to innovate and adapt quickly to market changes is a key advantage in today’s fast-paced business environment.
Enhancing Decision-Making and Overall Performance Through Engaged Leadership
Leadership plays a pivotal role in the success of Lean initiatives. When leaders are engaged and lead by example, it motivates the entire organisation. I worked with an executive team that participated in Lean training alongside their employees. This united approach broke down barriers and improved communication, resulting in faster decision-making and an increase in overall productivity. Engaged leaders also foster a culture of trust and collaboration, which is essential for sustaining long-term improvements.
Key Takeaway(s)
The manufacturing landscape in the UK is more competitive than ever, but with challenges come opportunities for those willing to adapt and evolve. Embracing Lean Coaching and Mentoring isn’t just about tweaking processes—it’s about transforming your entire operation.
By supercharging operational performance and efficiency, you unlock immediate benefits in cost savings and speed. Fostering a culture of continuous improvement ensures that these gains are not just temporary boosts but part of a sustained trajectory of growth. And by gaining a competitive edge in the market, you position your company not just to survive but to thrive amid industry changes.
From my own experiences working with manufacturers across the UK, the most remarkable transformations occur when companies invest in their people as much as their processes. Lean coaching empowers teams, breaks down silos, and cultivates leaders at every level.
So, if you’re ready to unlock success and transform your manufacturing operations, consider the profound impact that Lean project coaching and mentoring can have. The journey towards excellence is ongoing, but with the right guidance and commitment, the rewards are unparalleled. By embracing this approach, you not only enhance your operational capabilities but also build a resilient organisation poised to meet the challenges of tomorrow. The future of manufacturing is bright for those who dare to innovate and invest in their most valuable asset—their people. As the industry continues to evolve, those who prioritise continuous improvement and employee development will find themselves at the forefront of innovation and success. IF you’d like to know more about our Lean Coaching and Mentoring Programme – Click Here
More Blog Posts
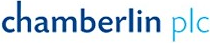
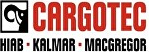
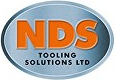

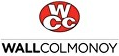
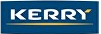
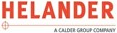
To leave me a message or book a return call at a time that suits you