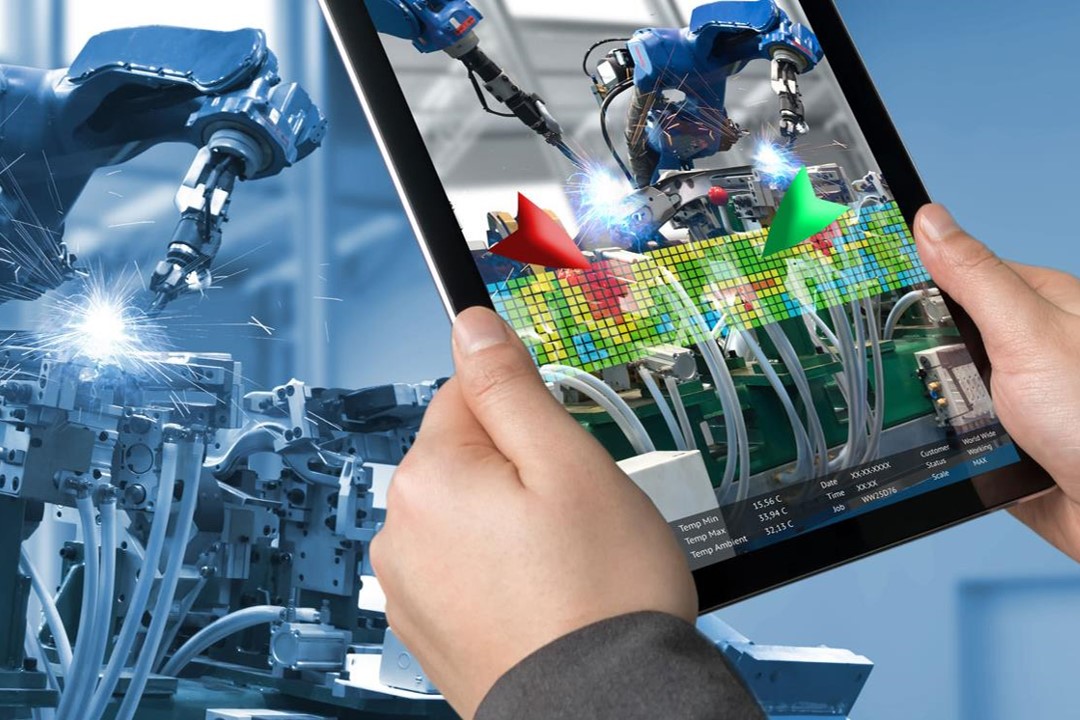
7 Digital Technologies That Will Transform Your Factory
What is Digital Manufacturing?
Digital manufacturing is a term that describes how technology has changed the way we design, build, and produce products. The connected capabilities of a digital factory present several opportunities for manufacturers to gain scalable agility, flexibility and operational performance.
It brings together Information Technology and Operational Technology, resulting in manufacturing processes that are enabled by cyber-physical capabilities. This convergence ensures companies get actionable insights at a glance, which helps to bridge the gap between isolated processes and operational transparency to increase performance.
Here we look at 7 technologies that can transform manufacturers on their journey to digital
Industrial Internet of Things (IIoT)
The Industrial Internet of Things (IIoT) is a vision for the future of manufacturing that aims to link all devices, machines, and systems together through digital networks.
The IIoT represents a significant shift in how manufacturing will be done in the future. Digital technologies are already changing how products are made and delivered, but the Industrial Internet of Things promises to take these changes further by connecting all aspects of industrial processes, from design to production and delivery.
Industrial internet of things (IIoT) is an emerging technology that has been designed to connect objects such as machines and sensors through wireless networks or wired connections. The purpose behind this is to allow different devices to communicate with each other in order to carry out complex tasks which would otherwise require human interaction. For example, if there was a sensor on a machine which detected that it was overheating then it could send this information back to its central server which would then be able to shut down the machine before any damage occurred.
Big Data and Analytics Tools
Big data and analytics tools are increasingly being used in digital manufacturing. The technology is expected to play an ever-increasing role in the development of products, as well as in their production.
The ability to gather and process data from various sources, including sensors and other devices, is one of the key benefits of digital manufacturing. When combined with artificial intelligence (AI), big data and analytics can provide valuable insights that enable companies to improve product quality, reduce costs and enhance customer satisfaction.
Manufacturing Execution Software
Manufacturing Execution Software (MES) is a software application used by manufacturers to monitor and control manufacturing processes. It includes all aspects of the production process, from the moment raw materials enter the facility until they are shipped out. MES systems can be used to manage both discrete and batch processes, as well as continuous ones.
Manufacturing execution system is an integrated software platform that automates and integrates various functionalities within a manufacturing environment. It is based on modern IT technologies (e.g. web services, XML), which enable flexible integration into existing production systems and provide easy access to information from external systems such as ERP or CRM systems. MES enables companies to improve their competitiveness by increasing efficiency, increasing throughput, reducing costs, and enhancing quality control by using real-time data from all operational areas of the enterprise.
Check out our very own sister company FactoryIQ MES software here
Advanced Robotics
Robotics is a rapidly growing field with new innovations in technology and capabilities. Advances in micro-electro-mechanical systems (MEMS) are making it possible to have smaller sensors and actuators that can be used in small spaces. This means that companies can now create robots that can be used in environments where they could not previously go.
Advances in artificial intelligence (AI) are also having an impact on robotics. AI has been around for decades, but now it is more powerful than ever before due to advances in computer hardware and software. The combination of AI and robotics is opening up new possibilities for automation that were not possible before due to limitations.
Sensing Technology are also driving changes in how we think about automation. In the past, most sensor technologies were based on electromechanical components like gears or switches that respond when there is a change in position or force applied to them by another object or person. Today’s sensors are based on MEMS technology which has allowed us to develop sensors that can detect temperature changes, motion, pressure, vibration and other physical phenomena. Other advances have seen programmable sensors via the use of apps with multiple actions similar to the Zapier style application for automated task in software, the ‘If this do that’ scenario.
Advanced robotics for manufacturing is the most powerful tool for productivity, flexibility and innovation in the modern factory. Robotics technology is evolving rapidly and the ability to easily integrate new capabilities into existing processes is essential.
Robots are already well-suited for repetitive tasks that require very high precision. But they can also handle a wide variety of other tasks in the factory, including: Material handling, Assembly, Testing & inspection, Packaging & labelling, and more.
Additive Manufacturing
Additive manufacturing is a type of manufacturing process that creates a three-dimensional object based on a digital file. This is done by laying down successive layers of material and then fusing them into place with heat. The technology can be used to produce parts and products ranging from the smallest medical devices to the largest airplane parts.
The technology has been around for decades, but it’s only recently become affordable and available to consumers.
Now that 3-D printers are becoming more common, experts are looking at how they could be used in manufacturing. Many companies are using additive manufacturing to make products or parts that would normally be made by injection moulding or other processes.
Additive manufacturing can also be used to make prototypes of new products in just hours or days instead of weeks or months. This makes it easier for companies to test out new designs before going into full production with them.
Digital Twins
Digital Twins for manufacturing are a new concept that is being widely adopted by today’s manufacturers. The digital twin of a manufacturing plant is a virtual representation of the real-world equipment, processes, and environment. It is a virtual representation of the physical world in which everything can be seen, monitored, controlled, and analysed in real time.
The concept of Digital Twins was anticipated by David Gelernter’s 1991 book Mirror Worlds. Since then, it has become an essential part of industrial applications across various industries.
Digital Twins have the potential to transform businesses by providing valuable insights into their facilities that can help them improve performance and make more informed decisions about resource allocation. These insights provide opportunities for companies to optimise their operations and identify bottlenecks that may affect productivity or lead to losses in revenue.
Augmented Reality
Augmented reality (AR) is a technology that overlays a computer-generated image on a user’s view of the real world, thus providing a composite view. Augmented reality enhances one’s current perception of reality, whereas virtual reality replaces the real world with a simulated one.
Augmented Reality and Digital Twin technologies go hand in hand. With augmented reality, you can overlay your digital twin onto the real world. This way you can see what your machine looks like as close to your real-world environment. This will give you more insight and help you make better decisions about future upgrades.
Takeaway:
The digital era has brought about revolutionary changes to all kinds of industries, and manufacturing is no different. As a tool for improving productivity, efficiency, and quality control, digital technology is becoming increasingly important for manufacturers. Many manufacturers are starting to see it as a valuable asset that can improve their output and their bottom line.
If you need support in anything Growth, Strategy or Operations don’t hesitate to get in touch.
More Blog Posts
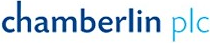
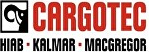
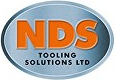

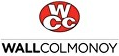
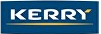
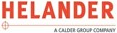
To leave me a message or book a return call at a time that suits you