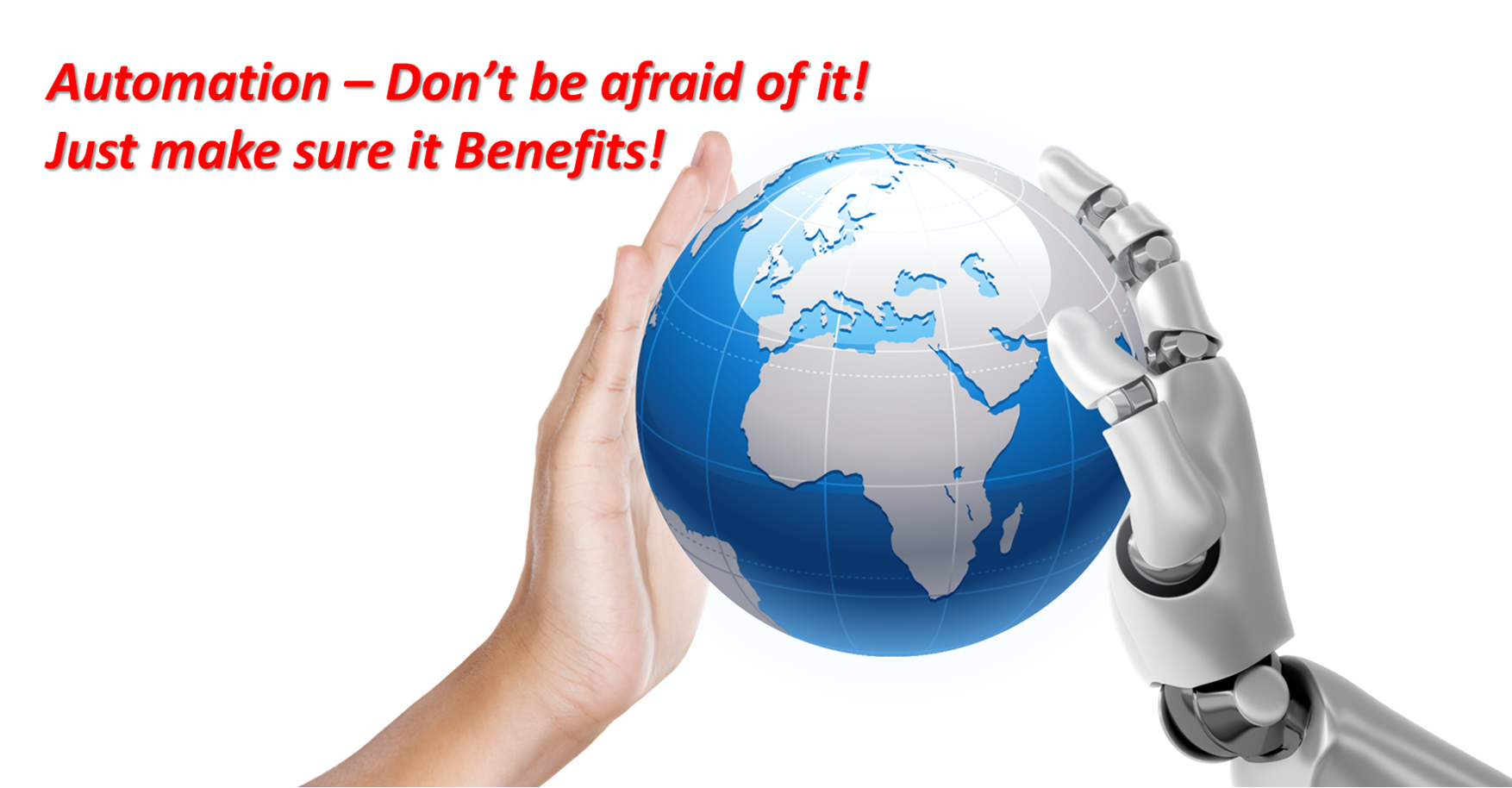
Automation – Don’t shy away from it.
Automation has been a cornerstone of manufacturing for years, evolving through numerous forms and innovations. This blog post delves into the significant advantages that automation, when combined with creative thinking and Lean Principles, can bring to businesses. It emphasises that while automation should not be shied away from, it is crucial to understand its impact, benefits, and justification for your business through thorough analysis.
The Evolution and Importance of Automation
Automation is not a novel concept. Its roots can be traced back to the Industrial Revolution when machinery began to replace manual labour, dramatically increasing efficiency and production capacity. Over the decades, automation has continued to evolve, incorporating advanced technologies such as robotics, artificial intelligence, and the Internet of Things (IoT). These advancements have transformed manufacturing, enabling higher precision, faster production times, and reduced human error.
In the mid-90s, as a Kaizen Engineer with McKechnie Plc, I witnessed firsthand the transformative power of automation. We invested in machines capable of auto-ejecting or unloading parts once a cycle was completed—a process known as Hanedashi in Lean terminology. This simple yet effective device saved associate time by allowing the machine to handle the unloading process, enabling the associate to focus on loading the next part. This innovation laid the foundation for Single Piece Flow production lines, also known as Chaku Chaku Lines.
The Mechanics of Single Piece Flow and Chaku Chaku Lines
Single Piece Flow, or Chaku Chaku (which translates to “Load Load” in Japanese), is a Lean manufacturing approach where each machine in a production line is loaded with parts sequentially. All necessary machines are positioned close together, forming a cell that facilitates seamless workflow. The goal is to minimise work-in-progress (WIP) and ensure that each part moves through the production process without delays.
In a Chaku Chaku Line, automation is employed wherever possible to streamline operations. For example, loading a part into a machine may require precise orientation and proper seating in a jig, tasks that typically demand human skill. However, once the machine cycle is complete, the part can be automatically ejected, eliminating the need for manual intervention. This approach not only improves efficiency but also reduces the risk of errors and defects.
Jidoka: Automation with Human Intelligence
Another critical concept in Lean manufacturing is Jidoka, one of the two pillars of the Toyota Production System, along with Just-In-Time (JIT). Jidoka, often referred to as “automation with a human touch” or “autonomation,” involves integrating human intelligence into automated processes. The essence of Jidoka is to enable machines to detect and respond to problems autonomously, ensuring that production stops immediately when a defect or issue is identified.
By incorporating Jidoka, manufacturers can address the root causes of defects, leading to continuous improvements in product quality and process efficiency. This approach empowers equipment to distinguish between good and defective parts without constant human monitoring, further enhancing productivity and reducing waste.
Real-World Applications and Benefits
The implementation of Load Load Lines and Autonomation yields substantial benefits, including the elimination of WIP, defect-free production, and significant productivity gains. For instance, an associate can manage multiple machines simultaneously, a practice known as multi-process handling, thereby optimising labour utilisation.
In my experience at McKechnie Plc, we established a highly efficient production cell, not so creatively named Cell 7, which manufactured fasteners. The traditional production route involved multiple stages, including Header Machine, Turn, Centreless Grind, Fillet Roll, and Thread Roll, with parts moving as batches through various departments. This approach was fraught with inefficiencies and waste.
By adopting the principles of Single Piece Flow, Load Load Lines, and Autonomation, we transformed Cell 7 into a fully autonomous production line. The process began with bowl feeding fasteners into the system, after which the line handled everything else, from loading and unloading to quality inspection using visual cameras. This comprehensive automation minimised human intervention, with associates only required for machine consumables, tooling changes, and addressing any significant issues.
The Strategic Role of Automation in Modern Manufacturing
The integration of automation in manufacturing is no longer a luxury but a necessity for businesses aiming to stay competitive in a rapidly evolving market. The modern manufacturing landscape is characterised by increasing demand for customisation, shorter product life cycles, and heightened quality standards. Automation addresses these challenges by enabling manufacturers to produce high-quality products at scale, with greater flexibility and efficiency.
Customisation and Flexibility
One of the most significant advantages of modern automation is its ability to facilitate mass customisation. Advanced automated systems can be programmed to handle a wide variety of products and configurations without extensive downtime for retooling or adjustments. This flexibility allows manufacturers to meet diverse customer needs and respond quickly to market changes.
Quality Assurance
Automation also plays a crucial role in maintaining consistent quality. Automated systems equipped with sensors, cameras, and other monitoring devices can detect defects and deviations in real-time, ensuring that only products meeting stringent quality standards proceed through the production process. This capability is particularly valuable in industries where precision and reliability are paramount, such as aerospace, automotive, and medical device manufacturing.
Efficiency and Productivity
Efficiency gains from automation extend beyond the production floor. Automated systems can optimise supply chain operations, inventory management, and logistics, reducing lead times and minimising the risk of stockouts or overproduction. These improvements contribute to overall productivity and cost savings, enhancing a company’s bottom line.
Overcoming Barriers to Automation
Despite the clear benefits, some businesses remain hesitant to embrace automation due to perceived barriers such as cost, complexity, and potential job displacement. However, these concerns can be addressed through strategic planning, careful analysis, and a focus on long-term gains.
Cost Considerations
While the initial investment in automation technology can be substantial, the long-term benefits often outweigh the costs. Businesses should conduct a thorough cost-benefit analysis to assess the potential return on investment (ROI). Factors to consider include increased production capacity, reduced labour costs, improved quality, and shorter cycle times. In many cases, the savings and efficiencies gained through automation can lead to a rapid ROI.
Skill Development and Workforce Transition
Another common concern is the impact of automation on the workforce. While automation can reduce the need for certain manual tasks, it also creates opportunities for new roles that require advanced technical skills. Companies can mitigate job displacement by investing in training and development programs to upskill their employees, preparing them for higher-value tasks such as programming, maintenance, and quality control.
Complexity and Integration
Integrating automation into existing processes can be complex, particularly for businesses with legacy systems. However, advancements in technology have made it easier to implement and integrate automated solutions. Collaborative robots (cobots), for example, are designed to work alongside human operators, enhancing productivity without the need for extensive modifications to existing workflows. Additionally, modular automation systems can be scaled and adapted to meet evolving needs.
The Future of Automation in Manufacturing
The future of manufacturing is undeniably intertwined with the continued advancement of automation technologies. Emerging trends such as Industry 4.0, the Industrial Internet of Things (IIoT), and artificial intelligence (AI) are set to further revolutionise the sector.
Industry 4.0 and the Smart Factory
Industry 4.0 represents the fourth industrial revolution, characterised by the integration of digital technologies into manufacturing processes. This paradigm shift encompasses the use of IoT devices, data analytics, and AI to create smart factories where machines communicate and collaborate autonomously. These connected systems enable real-time monitoring, predictive maintenance, and data-driven decision-making, leading to unprecedented levels of efficiency and flexibility. This is something our sister company offers FactoryIQ – The Smart Factory Made Simple
Artificial Intelligence and Machine Learning
AI and machine learning are poised to play a transformative role in manufacturing automation. These technologies can analyse vast amounts of data to identify patterns, optimise processes, and predict potential issues before they occur. For example, AI-driven predictive maintenance can significantly reduce downtime by identifying when equipment is likely to fail and scheduling maintenance proactively.
Collaborative Robotics
Collaborative robots, or cobots, are designed to work safely alongside human operators, enhancing productivity and flexibility. Cobots can handle repetitive, hazardous, or ergonomically challenging tasks, allowing human workers to focus on more complex and value-added activities. As cobot technology advances, their capabilities and applications will continue to expand, making them an integral part of the modern manufacturing landscape.
Additive Manufacturing
Additive manufacturing, commonly known as 3D printing, is another technology that complements automation. It enables the production of complex and customised parts with minimal waste and reduced lead times. When integrated with automated systems, additive manufacturing can streamline prototyping, reduce inventory costs, and accelerate product development cycles.
Case Study: Transforming Manufacturing with Automation at McKechnie Plc
To illustrate the impact of automation in a real-world setting, let’s revisit the case of McKechnie Plc, where I worked as a Kaizen Engineer in the mid-90s. Our journey with automation began with the introduction of Hanedashi devices, which automated the unloading of parts from machines. This initial step laid the groundwork for more extensive automation initiatives.
Setting Up Single Piece Flow and Load Load Lines
Recognising the potential of Single Piece Flow, we restructured our production lines to create Chaku Chaku Lines. By co-locating all the machines needed for a product in a single cell, we minimised the time and effort required for material handling. Automation played a crucial role in this transformation, with machines automatically ejecting finished parts and readying themselves for the next cycle.
Implementing Autonomation for Quality Assurance
To further enhance our production process, we integrated Jidoka principles, enabling machines to autonomously detect and respond to defects. Visual cameras were installed to inspect parts in real-time, ensuring that only high-quality products moved forward in the production line. This autonomation approach not only improved product quality but also reduced the need for manual quality checks, freeing up associates to focus on other tasks.
Achieving Full Autonomy with Cell 7
Cell 7, our fastener manufacturing cell, became a showcase of automation excellence. By combining Single Piece Flow, Load Load Lines, and autonomation, we achieved a fully autonomous production process. Fasteners were bowl fed into the system, and the line handled everything from loading and unloading to quality inspection and defect rejection. Human intervention was required only for machine consumables, tooling changes, and addressing significant issues.
Results and Benefits
The results of our automation efforts were nothing short of remarkable. We experienced a significant reduction in work-in-progress, virtually eliminating delays and bottlenecks. Product quality improved dramatically, with defects identified and addressed in real-time. Productivity soared as associates could manage multiple machines simultaneously, optimising labour utilisation. Overall, the integration of automation led to substantial cost savings, higher efficiency, and enhanced competitiveness.
Conclusion: Embracing Automation for a Competitive Edge
Automation, when combined with creative thinking and Lean Principles, offers immense benefits to businesses. From improving efficiency and productivity to enhancing product quality and flexibility, the advantages are clear. However, it is essential to approach automation strategically, conducting thorough analysis to understand its impact and justify the investment.
As the manufacturing landscape continues to evolve, staying ahead of the curve requires embracing automation and leveraging advanced technologies. By doing so, businesses can unlock new levels of performance, reduce costs, and remain competitive in an increasingly dynamic market.
At TCMUK Limited, we are committed to helping UK manufacturers embed strategies that reduce costs, increase sales, and boost profits. Our expertise in automation and Lean Principles enables us to guide businesses through the complexities of implementing and optimising automated systems. Whether you are looking to enhance your existing processes or embark on a comprehensive automation journey, we are here to support you every step of the way.
If you are ready to explore the transformative potential of automation for your business, contact us today to learn more about our services and how we can help you achieve your goals. Don’t shy away from automation—embrace it and unlock the full potential of your manufacturing operations.
0330 311 2820
More Blog Posts
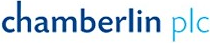
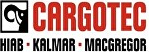
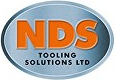

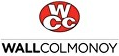
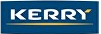
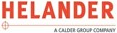
To leave me a message or book a return call at a time that suits you