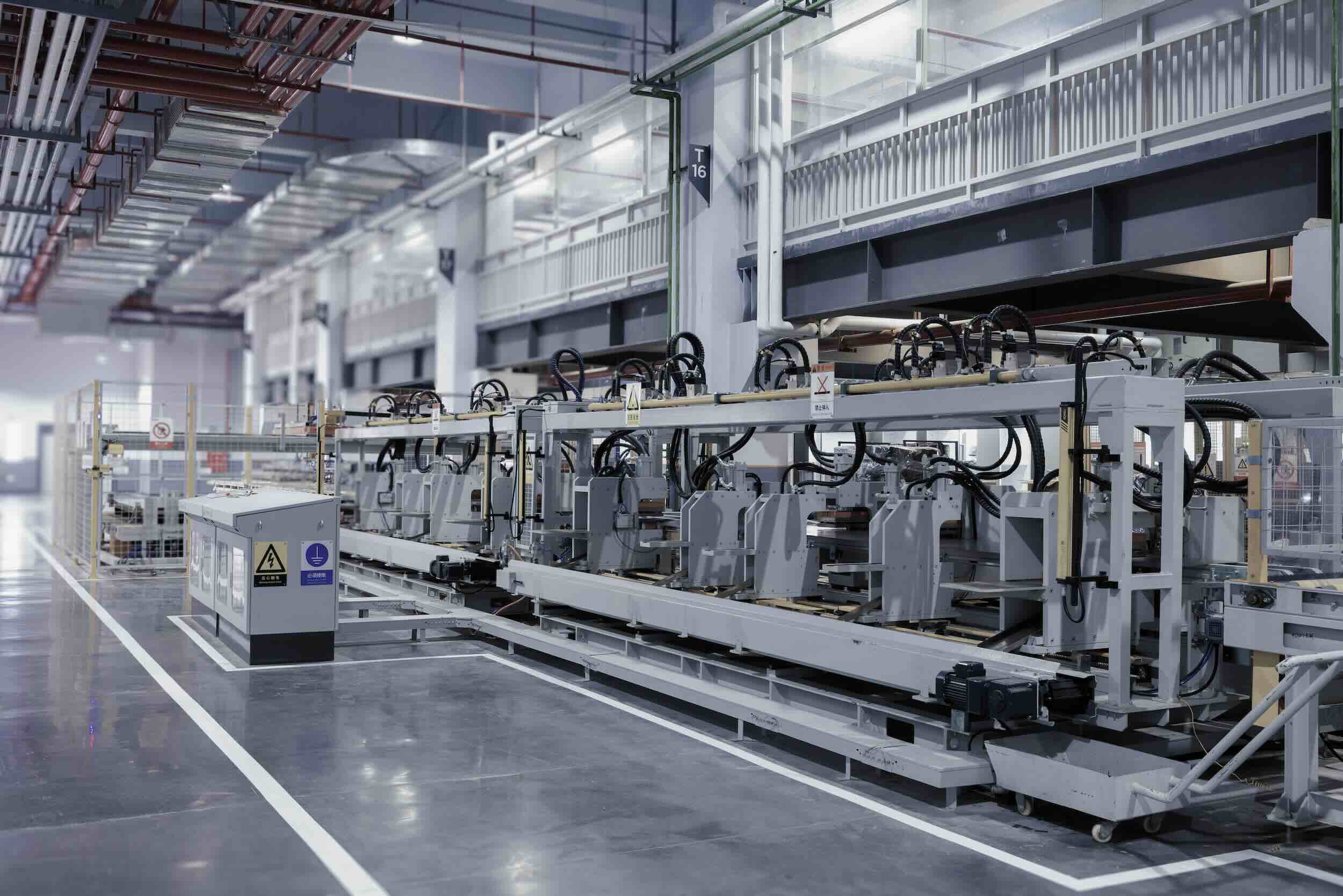
Embedding Lean Manufacturing: A Blueprint for Manufacturers’ Success
As a manufacturing professional in the UK, you’re likely all too familiar with the constant pressure to improve efficiency, reduce costs, and stay competitive in an increasingly global marketplace. Over the years, I’ve worked with numerous British manufacturers who have faced these challenges head-on, and time and time again, I’ve seen one approach stand out as a game-changer: lean manufacturing.
Lean manufacturing isn’t just another buzzword or passing trend. It’s a proven methodology that has transformed industries worldwide, and it’s particularly relevant for UK manufacturers looking to thrive. In this post, we’ll explore the essential steps to embed lean manufacturing in your business and highlight why so many manufacturers are embracing this approach. We’ll also look at some inspiring success stories that demonstrate the transformative power of lean principles.
Essential Steps to Implement Lean Manufacturing
Implementing lean manufacturing is a journey, not a destination. It requires commitment, patience, and a willingness to challenge the status quo. Here are the key steps you’ll need to take to successfully embed lean principles in your organisation:
a) Align your organisation around lean principles
The first and perhaps most crucial step is to ensure that everyone in your organisation understands and buys into the lean philosophy. This means educating your team about the core principles of lean manufacturing, such as:
- Identifying and eliminating waste
- Continuous improvement (Kaizen)
- Respect for people
- Creating flow in processes
In my experience, resistance to change is one of the biggest hurdles in implementing lean. That’s why it’s essential to communicate the benefits of lean manufacturing clearly and consistently. Emphasise how it can make everyone’s job easier, more satisfying, and more secure in the long run.
b) Map the value stream to identify waste
Value stream mapping is a powerful tool that helps you visualise your entire production process, from raw materials to finished product. By creating a detailed map, you can identify areas of waste, inefficiency, and bottlenecks.
I once worked with a UK-based casting manufacturer who was struggling with long lead times. Through value stream mapping, we discovered that components were spending an average of 15 days in various queues throughout the production process. By addressing these queues, we were able to reduce lead times by over 50%. (Reducing Lead-time Case Study)
c) Create flow and pull systems for smoother operations
Once you’ve identified areas of waste, the next step is to create flow in your processes. This means arranging your production line so that work moves smoothly from one step to the next, without unnecessary stops or delays.
Pull systems, such as Kanban, can be particularly effective in creating flow. Instead of pushing products through the system based on forecasts, pull systems produce items based on actual customer demand. This reduces inventory, improves cash flow, and ensures you’re making what customers actually want.
d) Utilise lean tools like 5S, Kanban, and Six Sigma
Lean manufacturing offers a variety of tools and techniques to help you improve your operations. Some of the most effective include:
- 5S (Sort, Set in order, Shine, Standardise, Sustain): A method for organising workspaces for efficiency and effectiveness.
- Kanban: A visual system for managing work-in-progress and scheduling production.
- Six Sigma: A data-driven approach to eliminating defects and reducing variability.
e) Foster a culture of continuous improvement
Lean manufacturing is not a one-time project; it’s an ongoing process of continuous improvement. Encourage your team to constantly look for ways to eliminate waste and improve processes. Implement a system for collecting and acting on employee suggestions.
f) Implement technology and automation to enhance lean processes
While lean manufacturing originated before the digital age, modern technology can significantly enhance its effectiveness. Consider implementing an Manufacturing Execution Software (MES) systems like FactoryIQ to improve visibility across your operations, or explore how Industry 4.0 technologies like IoT sensors and data analytics can support your lean initiatives.
Why Manufacturers Embrace Lean Manufacturing
Now that we’ve covered the ‘how’, let’s look at the ‘why’. There are compelling reasons why manufacturers across the UK are embracing lean principles:
a) Significant improvements in efficiency and productivity
Lean manufacturing can lead to dramatic improvements in efficiency and productivity. By eliminating waste and streamlining processes, you can produce more with less. I’ve seen manufacturers increase their output by 30% or more without adding additional resources.
b) Substantial cost reductions through waste elimination
Waste is expensive. By identifying and eliminating the eight types of waste (defects, overproduction, waiting, non-utilised talent, transportation, inventory, motion, and extra-processing), lean manufacturers can significantly reduce their costs. This is particularly crucial for UK manufacturers facing increased competition post-Brexit.
c) Enhanced customer value and satisfaction
Lean manufacturing isn’t just about cutting costs; it’s about delivering more value to your customers. By focusing on what the customer truly values and eliminating everything else, you can improve quality, reduce lead times, and enhance overall customer satisfaction.
d) Environmental benefits from reduced resource consumption
With the increasing environmental awareness, lean manufacturing offers significant sustainability benefits. By reducing waste and improving efficiency, you’ll naturally reduce your consumption of energy and raw materials. This not only helps the environment but can also improve your company’s image and appeal to environmentally conscious customers.
e) Competitive advantage in the marketplace
Being lean can give you a significant competitive edge. The ability to deliver high-quality products quickly and at competitive prices can help you win new customers and retain existing ones.
f) Increased employee engagement and morale
When implemented correctly, lean manufacturing can significantly improve employee satisfaction. By involving employees in problem-solving and continuous improvement, you empower them and make their work more engaging. This can lead to higher retention rates and a more motivated workforce.
Real-World Success Stories
Let’s look at some inspiring examples of companies that have successfully embedded lean manufacturing principles:
Caterpillar Inc.’s lean journey and results
Caterpillar’s lean journey offers valuable lessons for manufacturers of all sizes. The company began implementing lean principles in the early 2000’s and has since seen remarkable results. Including the formalisation of its Caterpillar Production System which launched in 2005, and a strategic initiative to establish an enterprise-wide lean vision in 2012.
John Deere’s efficiency gains through lean principles
Another global manufacturer with operations in the UK, John Deere, has been on a lean journey since the 1990s. The company has reported significant improvements in productivity, quality, and employee satisfaction. In one facility, John Deere reduced the time to manufacture significantly through lean principles.
General Electric’s inventory reduction and quality improvements
GE’s adoption of lean principles, combined with Six Sigma, led to substantial improvements across its diverse business units. The company reported saving billions of dollars and significantly improving product quality.
While these are large multinational companies, I’ve seen similar results in smaller UK manufacturers. For instance, a medium-sized automotive parts manufacturer in the Midlands implemented lean principles and saw a 40% reduction in lead times and a 25% increase in productivity within 18 months.
Toyota’s pioneering lean practices
Toyota is often credited with pioneering lean manufacturing through its Toyota Production System (TPS). The company’s focus on continuous improvement and respect for people has led to unparalleled efficiency and quality. Toyota’s lean practices have been emulated by manufacturers worldwide, proving that lean principles can be adapted to various industries and scales.
Rolls-Royce’s lean transformation
Rolls-Royce, a renowned UK manufacturer, has also embraced lean manufacturing. By implementing lean principles, Rolls-Royce has achieved significant improvements in production efficiency and product quality. The company has reduced lead times, cut costs, and enhanced customer satisfaction, solidifying its position as a leader in the aerospace industry.
Conclusion
Embedding lean manufacturing is indeed a transformative process that can revolutionise your manufacturing operations. In following the key steps outlined – aligning your organisation, mapping value streams, creating flow, utilising lean tools, fostering continuous improvement, and leveraging technology – you can achieve significant improvements in efficiency, cost reduction, and customer satisfaction.
The benefits of lean manufacturing are clear and compelling. From improved productivity and reduced costs to enhanced customer value and environmental benefits, lean principles offer a pathway to long-term success and competitiveness.
As you embark on your lean journey, remember that it’s not about achieving perfection overnight. It’s about making consistent, incremental improvements that add up to significant results over time. Start small, celebrate your wins, learn from your setbacks, and keep pushing forward.
In the face of global competition and economic uncertainty, lean manufacturing offers UK manufacturers a proven approach to not just survive, but thrive. By embracing these principles, you can position your company for success in the years to come, driving innovation, efficiency, and growth in the ever-evolving manufacturing landscape.
Remember, the journey to lean manufacturing is challenging, but the rewards are well worth the effort. So, are you ready to start your lean journey and transform your manufacturing operations? The time to act is now. Embrace lean manufacturing and unlock the full potential of your business. By doing so, you will not only enhance your operational capabilities but also ensure a sustainable and prosperous future for your company in the competitive global market.
More Blog Posts
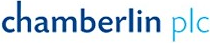
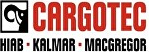
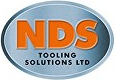

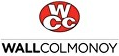
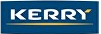
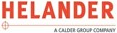
To leave me a message or book a return call at a time that suits you