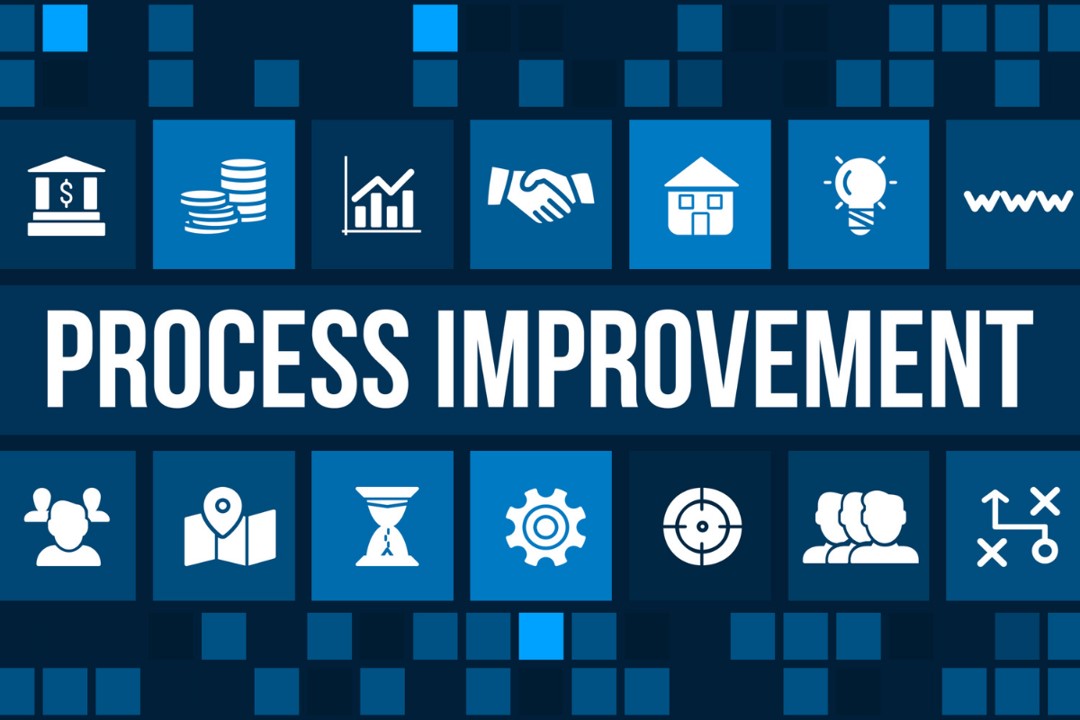
Driving Efficiency: The Role of Consistent Feedback in Manufacturing Process Improvement
Process improvement in manufacturing is all about identifying, analysing, and optimising existing business operations to meet new standards of efficiency and quality. A crucial component of this journey is the role of feedback – the consistent kind. When effectively harnessed, feedback offers significant opportunities to drive efficiency and improve performance across manufacturing processes.
The Concept of Feedback in Manufacturing
In the context of manufacturing, feedback represents a variety of inputs that provide insight into how operations are performing. These can come from varied sources, such as employees’ suggestions, customer feedback on product quality, or even technical data from machine sensors.
In an industry where precision and efficiency are paramount, each type of feedback can be invaluable. From pinning down inefficiencies in production lines to signalling the requirements for new capabilities, feedback provides the groundwork for beneficial changes.
Real-Time Feedback and Operational Efficiency
The potency of feedback is exponentially strengthened when it is received in real time. Real-time feedback eliminates lag time in data collection and analysis, enabling manufacturers to tackle inefficiencies head-on as they occur.
Consider the case of a major precision engineering manufacturer that utilised real-time machine data from FactoryIQ. Incorporating sensor technologies, they could instantly detect and address any deviations in machine performance. The result was significantly improved productivity, reduced waste, and heightened efficiency.
Feedback Loop: From Collection to Action
An efficient feedback loop encompasses timely collection, swift analysis, and effective implementation of insights derived from feedback. Feedback that is not acted upon (or not acted upon promptly) loses its impact.
Creating a feedback loop in manufacturing involves defining inputs, establishing collection channels, implementing analysis protocols, and setting up procedures for action based on these insights. It might seem complex, yet it’s a worthy investment that equips manufacturers with an ongoing resource for process improvement.
Continuous Feedback for Continuous Improvement
Manufacturing process improvement isn’t a one-off project; it’s an ongoing pursuit. This philosophy places continuous feedback at the core of sustained process improvement efforts.
Maintaining a consistent rhythm of feedback collection and analysis means you perpetually have your finger on the pulse of operational performance. With continuous feedback, manufacturers can identify patterns over time, predict potential challenges, and develop strategic actions to improve efficiency consistently.
Harnessing Technology to Facilitate Feedback
The feedback mechanism is greatly backed by technology. From data sensors on manufacturing equipment to software that automates customer feedback collection, various tools can facilitate feedback in manufacturing.
For instance FactoryIQ, our sister companies Manufacturing Execution Software (MES) can collect real-time data on machine performance, while FactoryIQ’s scheduling system can provide planning and customer feedback at various stages. Leveraging these technologies can lead to more consistent and accurate feedback, and by extension, more effective process improvements.
Additionally, FactoryIQ analytics tools (integrated into MES) can analyse feedback data to generate usable insights. These solutions utilise techniques including predictive analytics or machine learning, enabling manufacturers to extract meaningful conclusions from large volumes of feedback data.
Key Takeaways
Consistent feedback plays a pivotal role in enhancing manufacturing process efficiency. As a manufacturer, if you aren’t already placing feedback at the heart of your process improvement initiatives, it’s time you did.
The process might seem daunting, especially if you’ve traditionally relied on less feedback-oriented process improvement. But remember, like any new implementation, it takes time to set up and get used to. Once you overcome the initial hurdle, the benefits of consistent feedback can be substantial – marked improvements in efficiency, productivity, and ultimately, profitability.
Motivating your team to contribute, using technology to automate feedback collection and analysis, and creating an atmosphere where feedback is valued and acted upon, can go a long way in ingraining an Lean Thinking / Problem Solving culture that propels process improvement.
The manufacturing landscape is continually evolving and calls for continuous improvement. By tapping into the power of consistent feedback, you are arming your manufacturing operations with the capability to not just keep pace with this evolution but also to lead the charge.
The connection between consistent feedback and manufacturing process improvement is strong and direct. By acknowledging this and acting on it, you are solidifying the pathway towards greater efficiency and business success.
💡PS: If you’re a Manufacturer looking to Reduce Costs, Foster Innovation and Accelerate Growth please do get in touch here.
More Blog Posts
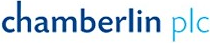
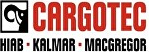
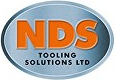

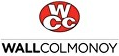
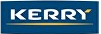
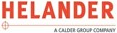
To leave me a message or book a return call at a time that suits you