By now, you’ve probably heard about Lean. It’s a powerful approach to management, which has its roots in manufacturing, but is used by many companies large and small to improve their processes and products.
As its name suggests, Lean is about eliminating waste — anything that doesn’t directly add value to the customer. This includes waste in time (waiting), materials (overproduction), money (overhead) and energy (people working on the wrong things).
Lean is a journey — not just a set of tools or tactics — and it takes time to become effective. But it can transform how you manage your people — giving you more time for important activities like coaching and developing your people so they can do their jobs better.
The Lean Leadership Journey
The journey to a Lean organisation is not an easy one. It requires a holistic approach and a complete mindset change. It takes time, effort and dedication to make the transformation successful. And it’s never over!
The following are some of the steps that you can take to start your journey toward becoming a Lean organisation:
Get everyone involved in the process. The Lean Transformation cannot be achieved through top-down management alone. The leader must work closely with employees at all levels to implement changes that will make the organisation more effective and efficient. Employees need to understand how they fit into this process, so that they can contribute effectively.
Set goals for improvement and measure progress toward those goals regularly. One of the primary reasons for implementing Lean practices is to improve business performance and increase efficiency, but measuring results will tell us if we’re moving in the right direction or not. We need to be measuring against specific goals set out at the beginning of the process (or before it began). This also helps us identify areas which need improvement as well as areas where we’re excelling.
The Lean Leaders Standard Work
Lean leadership Standard Work is a system that encourages continuous improvement and provides a framework for facilitating change. It requires leaders to focus on their actions, behaviours, and tools in order to drive continuous improvement in their organisation. This Lean Leadership Standard Work can be applied to managers, supervisors, directors, and executives alike.
Lean Leadership Standard Work encourages and promotes employees in organisations to reduce variation and improve performance. It also develops team members by demonstrating how to make smart changes and support people by defining what they should do when they take action.
Lean Leadership Standard Work can include:
- Develop process standards alongside the process operators
- Observing processes in action (Gemba Walks)
- Asking 5 Why questions
- Identifying gaps between standard & actual work (Audit)
- Supporting process improvement
- Coach and Mentoring Employees
- Empowering Accountability and Responsibility
- Deploying strategy
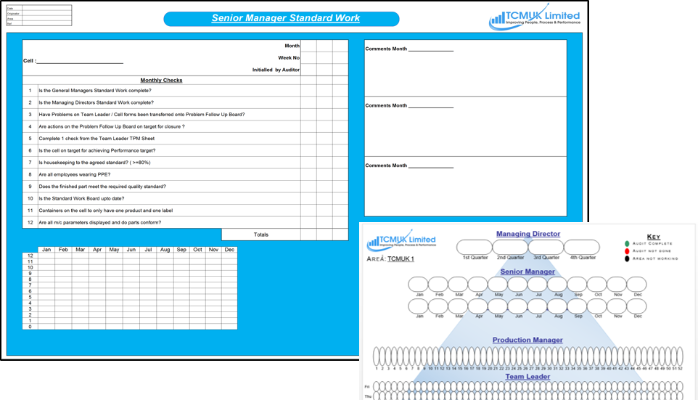
Lean Thinking as Leader
Lean Thinking as a Leader is about management that encourages you to make the most of your team and organisation. It is about creating an environment where people feel comfortable thinking “outside the box,” and where ideas can be considered, implemented, and monitored so that adjustments can be made quickly.
It requires leaders to be open-minded and encourages them to listen carefully to their team members’ ideas and suggestions. It also encourages leaders to collaborate with their teams in order to come up with better solutions for problems or issues. When everyone feels like they’re part of something bigger than themselves, they’ll be more likely to work hard toward achieving success in whatever it is they’ve been tasked with accomplishing.
The Lean Leader as a Teacher
A key concept in Lean is that people learn best by doing. Leaders must therefore create an environment where learning can happen, by encouraging employees to take on projects and responsibilities that stretch them, while also providing coaching and feedback along the way. The goal, according to Masaaki Imai (the author of Kaizen), is to help each employee become “Kaizen conscious, developing skills and tools for problem solving” — and this requires a great deal of effort on the part of managers in order to ensure that all employees are given opportunities to learn, grow and improve within their roles at work.
Eliminating waste is a key Lean Leadership Principle
Waste can be defined as anything that does not add value to the product or service being created. Waste occurs in all processes and can be categorised into three types of wasteful actions that negatively impact workflow, productivity and ultimately, customer satisfaction.
- Muda (or non-value-added work). These are activities that do not add any value to the end product or service, such as, Overproduction, Inventory, Defects, Motion, Over-processing, Waiting, Transportation.
- Muri (or overburden). This is when workers are asked to do more than they can handle efficiently, safely, or ethically.
- Mura (or unevenness). This occurs when there are unexpected fluctuations in demand for products or services due to things like seasonal change or competitor activity.
Waste takes time and resources to create, so eliminating it saves time and money.
Lean Leaders Put Customers First
Lean leaders are customer focused. They don’t waste time or money on anything that doesn’t directly improve the customer experience, and they know that this is the best way to grow their business.
This means that lean leaders put their customers’ needs first by:
- Listening to their customers and understanding their challenges and needs.
- Paying attention to what customers think about the product or service, and how they use it.
- Identifying areas where they can improve the products or services based on what customers say.
Takeaway: Lean leadership is about learning and improving.
A company benefits from having the right leadership in place, which ultimately helps a business to grow. They’ll learn from your customers, try new things, and challenge you in new ways. They’ll collaborate with others and actively seek outside support. Without good leaders, or without lean principles guiding those leaders, you’re going to get the same results: no learning and therefore no improvement.
Boost your team’s performance and your leadership potential with New Way Growth’s personalised Helping Managers to Succeed and Lead Programme. Let’s shape your leadership success story today!